Ever sensitive to global trends, the fashion world has already embarked on moves aimed at creating a sustainable society. Techniques such as the use of fermentation in indigo dyeing have developed in harmony with nature since time immemorial. And today, advances are being made in the development of new textiles using cutting-edge microbiological technology, such as amino acid synthesis, genetic modification, and macromolecular polymers. As such, a vision for a future in which fashion does not impose a burden on the environment has emerged.
Special Feature 1 – Microorganisms and Sustainability Report:
How advanced technology could transform the future of fashion
text by Rie Iizuka
Huge quantities of fibers and textiles are consumed in all kinds of settings, including clothing, motor vehicles, and homes. Chemical fibers such as polyester and nylon are, in most cases, mass produced from petroleum-derived raw materials that are not readily biodegradable. The production of wool and other animal-derived fibers entails the emission of large volumes of greenhouse gases in the process of raising the livestock that provide them, such as sheep and goats, while growing cotton and other fiber-yielding plants requires agrochemicals and large quantities of water. We must not overlook the environmental burden imposed by the fibers currently available to us, whether natural or chemical. As such, the development of new fibers that can be used for food, clothing, and housing will be essential in order to lead a sustainable lifestyle.
Success in developing new textiles
Based in the Yamagata Prefecture city of Tsuruoka, Spiber Inc. came into the limelight in 2013 as the first company to successfully develop a technology for mass-producing artificial spider silk from sugars with the aid of microbe-based fermentation. Natural spider silk is said to be 340 times stronger than steel and is believed to be the toughest fiber on the planet. The ability to artificially manufacture a fiber like this would likely reduce the burden on the environment in a variety of ways.
Spiber partnered with an outdoor clothing manufacturer to produce a prototype jacket made from its artificial spider silk, Qmonos. However, this fiber based on the genes in natural spider silk unfortunately turned out not to be suitable for apparel worn in harsh natural environments as, just like its natural counterpart, Qmonos exhibits a property called supercontraction, reducing in length by up to 50% when exposed to water.
Four years passed since Qmonos was developed. Spiber has succeeded in developing a new protein polymer.
Director and Representative Executive Officer Kazuhide Sekiyama was involved in research into protein structures from his undergraduate days and the development of Qmonos was also a product of his studies. Changing tack away from spider silk, he applied the same microbe fermentation technique in designing amino acid sequences suited to particular purposes. The result was Brewed Protein™ polymers, useful proteins manufactured by microorganisms via fermentation.
The manufacturing process is as follows. First, the amino acid sequence of the desired protein is designed and customized with reference to various natural proteins and the data accumulated by the company to date. Next, a proprietary algorithm is used to create the gene sequence on the computer. These genes are synthesized and introduced into microorganisms. In the culture process, the microorganisms ingest sugars and produce protein. To create a textile, the protein polymer (powder) produced by the refining process is turned into yarn and processed into a fabric (Figure 1).
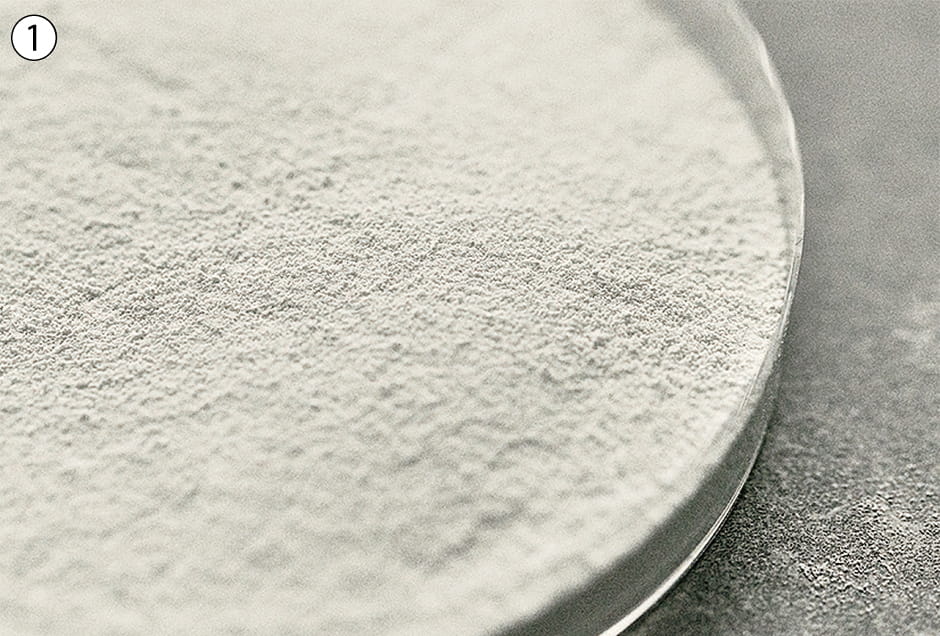
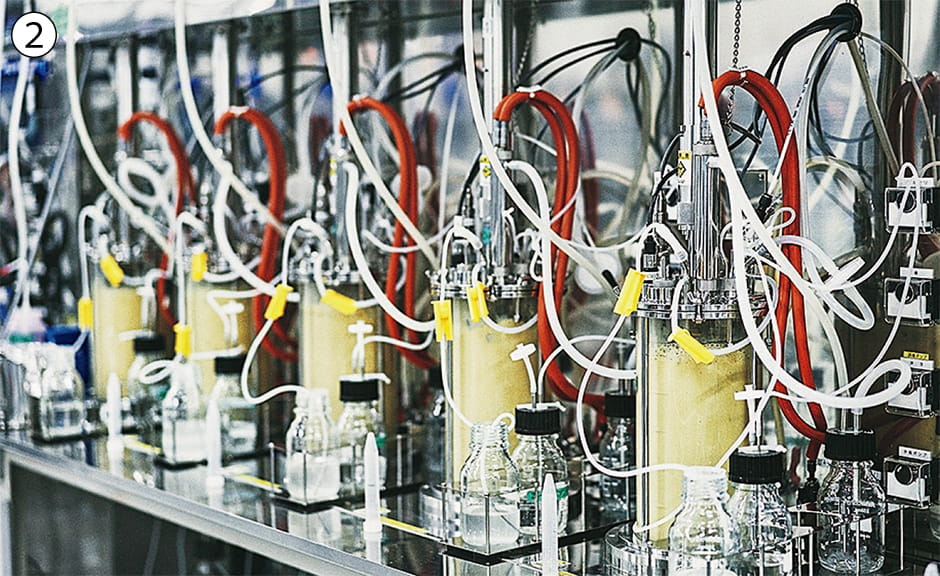
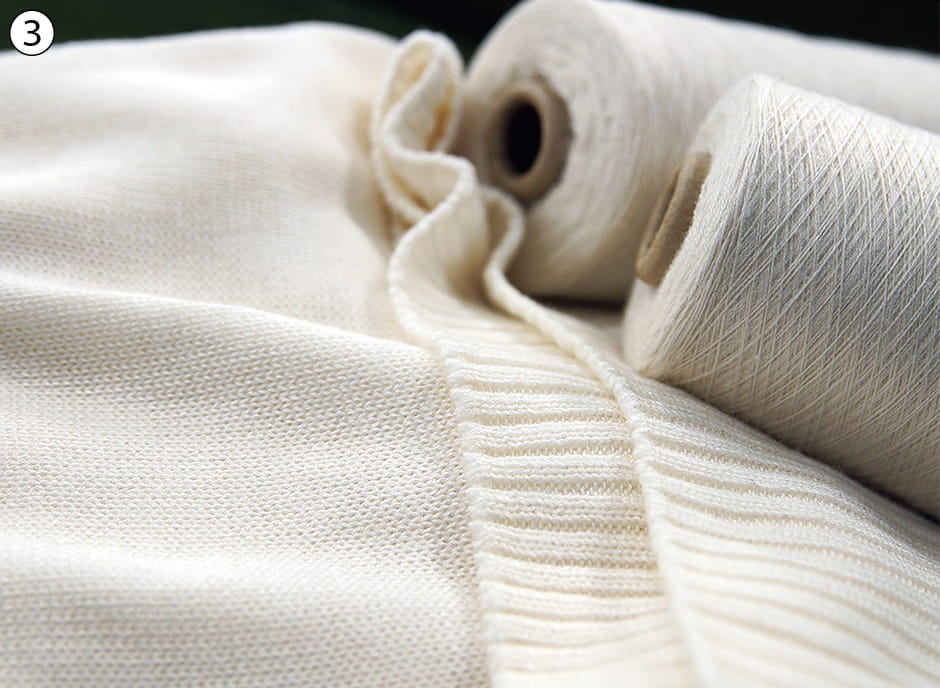
Figure 1. Brewed Protein™ materials produced by microorganisms① Brewed Protein™ polymer. This can be processed into various forms according to the usage and application.
② A small-scale microorganism culture device at Spiber’s lab in Yamagata, Japan.
③ A sample of knitwear using the spun yarn. Various textures can be obtained by altering the fiber diameter and protein content.
Advanced technologies are essential in order to produce protein using microbes, but Spiber also has unique technologies used in the yarn spinning process. The overall process of dissolving powdered raw material and turning it into fibers is similar to that used to manufacture petroleum-derived chemical fibers. However, in each case, “the individual parts of the process need to be optimized to suit the specific material. That’s because changing even one condition will naturally alter the properties of the finished fiber,” says Shota Togashi of the manufacturing team in Spiber’s Fiber and Textiles Division. The combination of protein design and processing method enables fibers with a variety of properties to be manufactured.
Microorganisms are essential to manufacturing fibers
Spiber is currently devoting its energies to developing fibers for apparel manufacturers, working with outdoor wear makers and even designers who show their collections at Paris Fashion Week. Winning plaudits for the tactile properties of its textiles, the company is gradually building up its presence in the fashion world, where sustainable materials are increasingly in demand.
Asked why he focused on the power of microorganisms in the development of Brewed Protein™ materials, Sekiyama explains, “It occurred to me that using highly energy-efficient microbes capable of multiplying at an unimaginably swift rate would enable us to conserve energy and resources in the manufacturing process, thereby minimizing both the environmental burden and production costs.”
In the course of development, he tested numerous different species, selecting carefully for factors such as production efficiency and stability, and ultimately chose one species as the cream of the crop. Brewed Protein™ fibers are currently used in such clothing as T-shirts and cashmere-like knitwear. While the target proteins that are manufactured may differ, the microorganisms used for fermentation are the same. However, there is apparently potential for considering other microorganisms for generating proteins tailored to the target substance for the development of artificial leather, fur, or hair, carbon fiber composites used in automotive components and the like, and products used in the medical field (Figure 2).
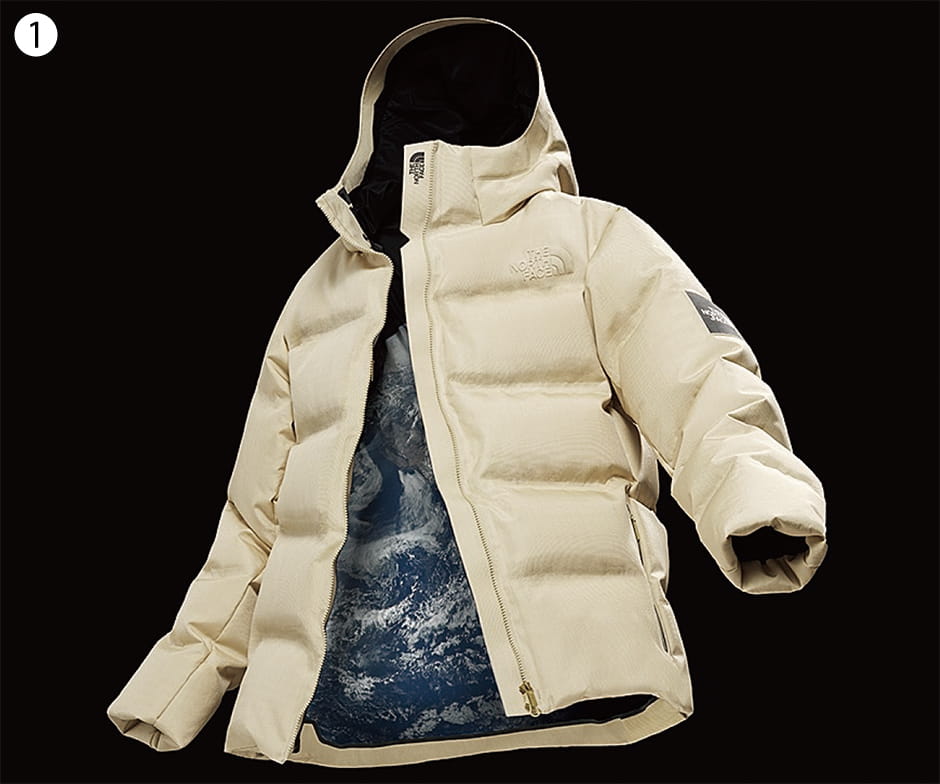
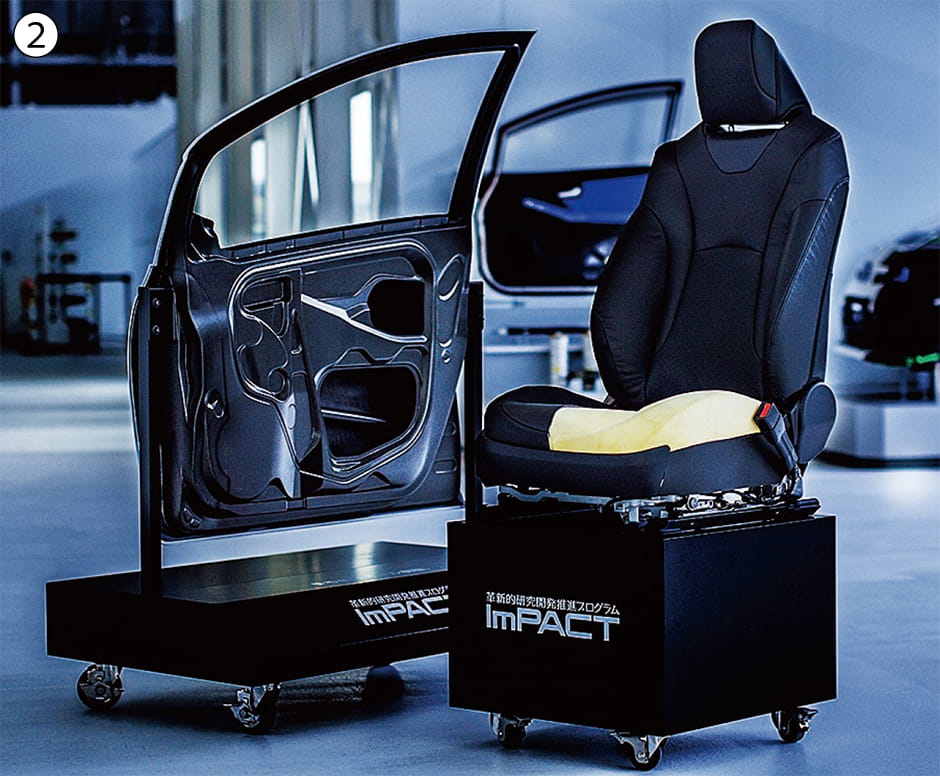
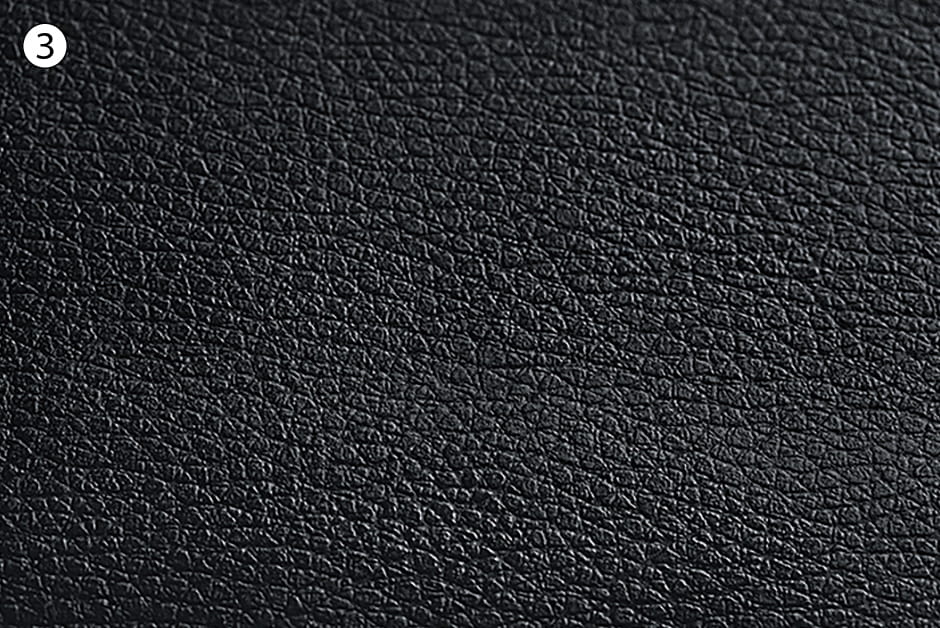
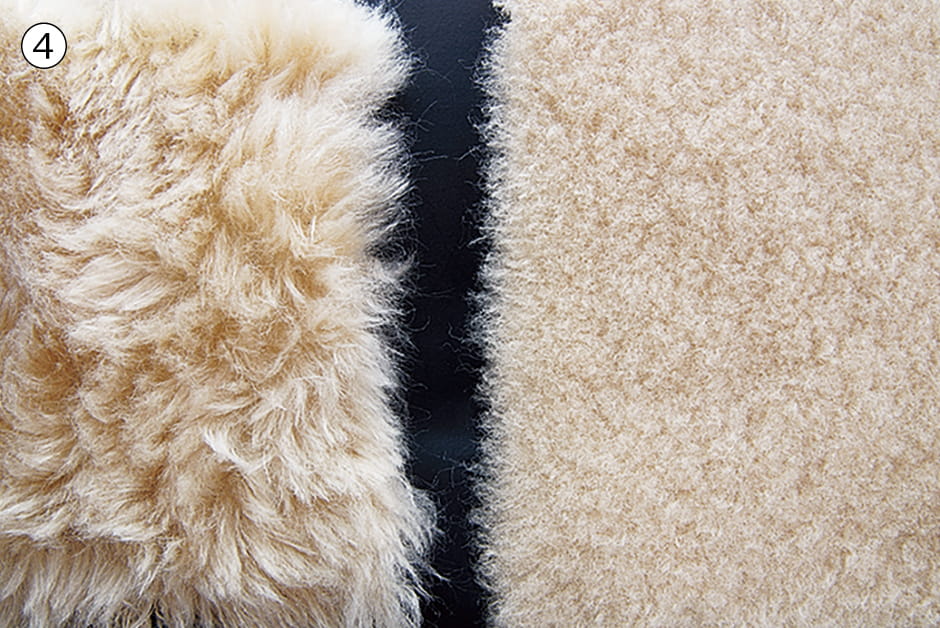
Figure 2. Products made from Brewed Protein™ polymers① A product resulting from joint R&D with Goldwin Inc. The Moon Parka is the world’s first outdoor jacket made from structural protein (*Moon Parka is a trademark of Spiber Inc. and Goldwin Inc.)
② These products were developed jointly with companies participating in the Impulsing Paradigm Change through Disruptive Technologies Program (ImPACT) promoted by the Cabinet Office (Figure courtesy of ImPACT).
③ A sample of a leather-like material formed by polymer processing of Brewed Protein™.
④ Samples of materials with furry textures created by processing short fibers of Brewed Protein™.
So essential to the process of manufacturing sustainable fibers are the microorganisms that the people from Spiber reflexively describe the microbes as “making them for us.”
As well as cases in which the substances produced by microbial degradation and fermentation are used, there are also endeavors to employ the power of decomposition to dispose of clothing without burdening the environment.
Osaka-headquartered fabric wholesaler V&A Japan Corp. has developed a biodegradable polyester called ReTE suitable for use in clothing. The company has developed a mechanism in which microorganisms in compost secrete enzymes that act with H2O and the heat of fermentation to hydrolyze the polyester, turning it into small molecules and ultimately breaking it down and returning it to the soil.
First of all, let us explain polyester in simple terms. The word “polyester” covers a diverse array of types of polyester. Broadly speaking, there is the polyester fiber used in clothing and the like, and the molded polyester used in such products as polyethylene terephthalate (PET) bottles. Incidentally, it is the latter kind that is used to make fleece fabrics.
Polyester is the most commonly produced synthetic fiber and is used in a variety of types of apparel, from sportswear to business shirts and underwear. Abrasion-resistant, durable, and quick-drying, not to mention lightweight and wrinkle resistant, polyester’s high-performance properties make it ideal for a wide range of uses. It is prized for use in clothing because it can withstand repeated washing, ironing, tumble-drying, and exposure to sunlight.
V&A Japan has succeeded in creating a material that combines this outstanding durability with the almost contradictory property of biodegradability.
Polyester biodegradable in specific compost
In fact, there are a number of other biodegradable polyesters (polylactides). Some are used in such items as disposable food containers and marketed under the name “biodegradable plastics,” while others are used in surgery as dissolvable stitches, a type of suture that does not require removal because it dissolves in the body. As such materials are based on the assumption that they will only be needed for a limited amount of time before being disposed of, their durability does not really come into question. Each country has its own organization that certifies biodegradability, requiring certain standards to be met regarding biodegradability, metal content, and the like. For example, one of the biodegradability standards relates to the carbon produced by microorganisms; Japan requires an increase of at least 60% in the quantity of carbon within six months of the test commencing, while some countries specify that the increase must be at least 90%.
V&A Japan’s product, on the other hand, retains its original properties even after washing and ironing, but takes around 12 months to decompose almost completely. This is why V&A Japan describes its product as “polyester biodegradable in specific compost” (Figure 3).
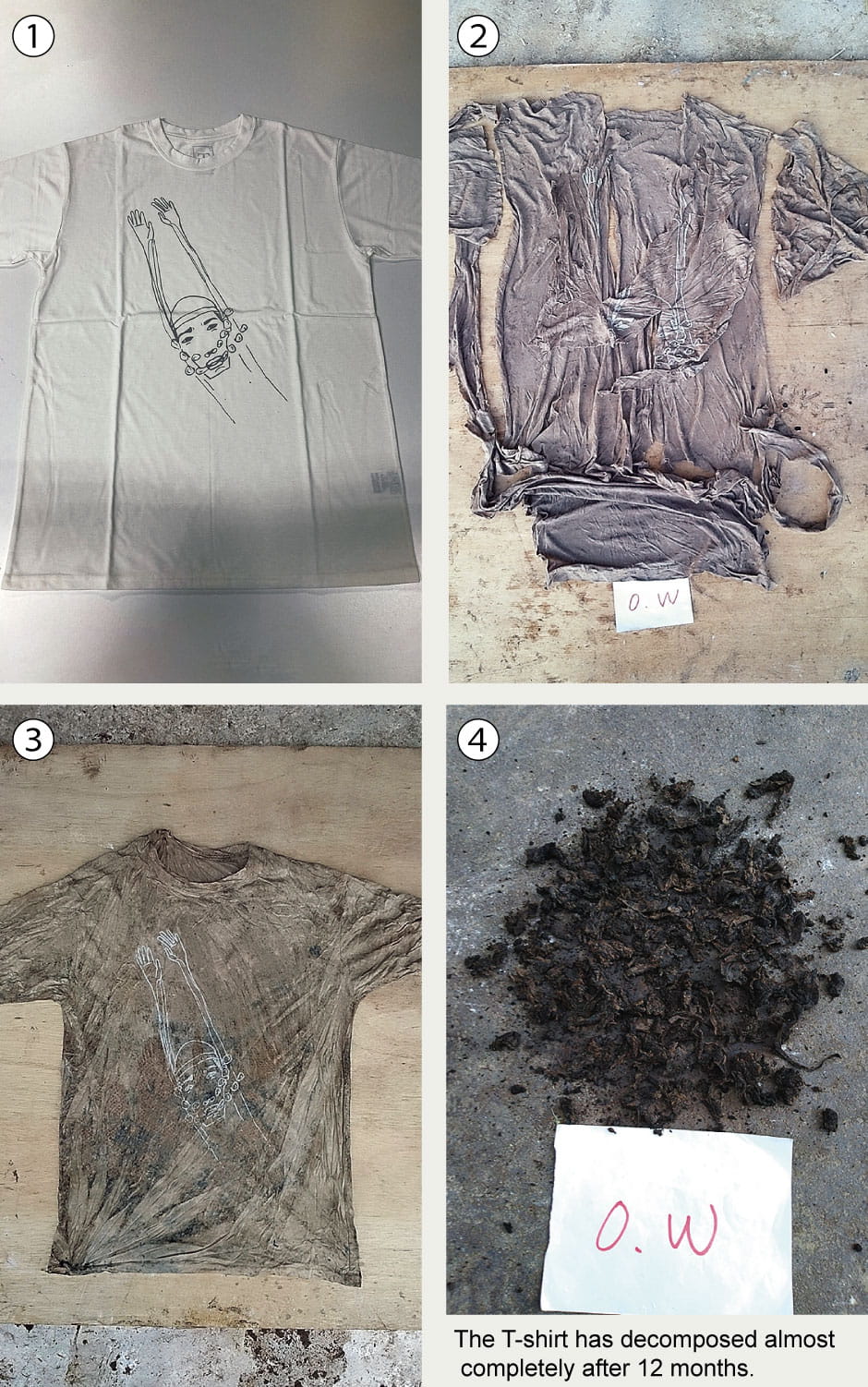
Figure 3. Decomposition test at a composting facility
The word “specific” is used here for a reason. As the company developed the product with biodegradability in mind, it researched not only molecular structures, but also, via repeated trial and error, locations in which it would decompose. The sites tested included anaerobic soil, pig farms, crop fields, and flower beds, but the location they ultimately settled on was a composting facility that also operates as a dairy farm.
“We experimented with various locations, but none of the others provided the results we were hoping for,” says Sawako Maki of V&A Japan’s Textile Sales Business Division.
This composting facility collects cattle manure and garbage, which it uses to produce compost. The compost is agitated every day, making it aerobic, with cattle manure and other food for the microorganisms also added daily. Fermentation raises the temperature of the compost to as high as 60-80°C.
Developed in partnership with polymer researchers, V&A Japan’s product achieves both biodegradability and the durability conferred by the structure of the resin, but the particular kind of microorganism causing its decomposition has not yet been identified. The company did decomposition tests using the same soil in a different place, but the fabric hardly decomposed at all. It is likely that the meticulous management of the composting facility creates an environment in which microorganisms thrive.
The key feature of this endeavor was that the company sought to put in place a mechanism covering not only the sale of the product, but also its recovery and decomposition. Once the clothing made with the fiber is no longer needed, it is collected by the sales outlet or the company itself, with V&A Japan overseeing the decomposition process at the facility. As the fabric looks no different from ordinary polyester, special tags are attached to the clothes to assist in its identification.
Overseeing the process through to final decomposition
One designer was so impressed by this initiative that, under her own brand, she launched the Compostable range of clothing (Figure 4), which uses only V&A Japan’s fabric. “The fashion world has traditionally used a lot of resources, but we need to think about sustainability,” says wmg. designer Junko Sakayori. “I agree with what this company’s trying to do, and at the same time, I’m pleased to be able to reduce the burden on the environment using polyester, as it’s a fabric offering a wide range of design possibilities, with few constraints on processing.”
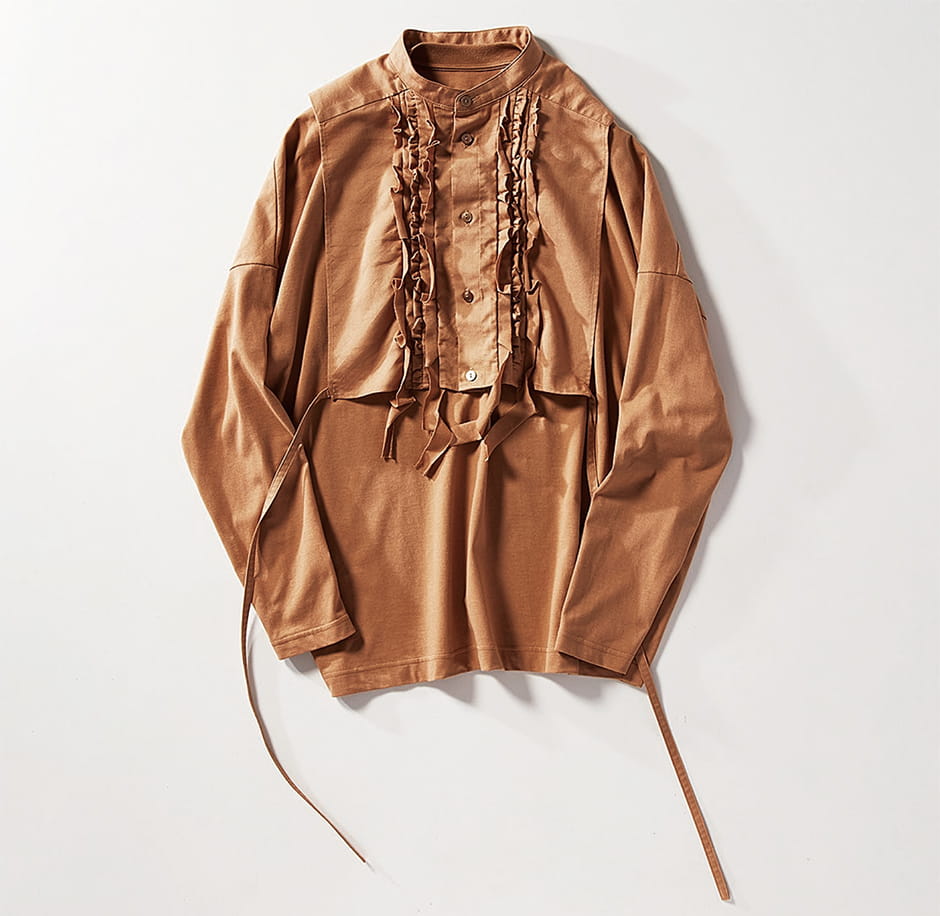
Figure 4. A T-shirt made from biodegradable polyesterFascinated by this material, Junko Sakayori launched her Compostable range.
Why did V&A Japan choose to oversee the whole process through to final decomposition?
In fact, biodegradable fabrics do not simply biodegrade everywhere and require specific locations for decomposition, depending on the material, with some decomposing in the ocean and others in landfill sites. Furthermore, there are anaerobic and aerobic landfill sites, the microorganisms living in which differ. Different microorganisms prefer different sources of food and decompose different things. In other words, a material will not necessarily decompose anywhere in the natural environment just because it is biodegradable. Indeed, there is a strong possibility that material decomposed by microorganisms that prefer anaerobic soil will not decompose in aerobic soil. However, as most consumers do not understand the situation to this extent, they tend to unthinkingly assume that biodegradable means an item returns to the soil.
“Since we’ve gone to all the trouble of making a biodegradable material, we thought we should take proper responsibility for it all the way through to final disposal,” says Maki. “We also want consumers to understand more about the fabrics used in clothing.”
So it seems that, while we can borrow the power of microorganisms, we will not be able to create a sustainable environment unless we also change our way of thinking.