世の中の動きに敏感なファッション業界は、すでにサステイナブルな社会に向けて動き出している。発酵を利用する藍染めなどは、古くから自然と調和しながら発展してきた。そして、現代においては、アミノ酸合成や遺伝子組み換え、また高分子ポリマーなど、微生物の先端技術による新たな繊維素材の開発が進んでいる。環境に負荷をかけないファッションの未来像が浮かび上がってきた。
特集 微生物とサステイナブル ルポ
先端技術が可能にするファッションの未来像
文/飯塚りえ
衣類、自動車、住宅などあらゆる場面で大量に消費される繊維。ポリエステルやナイロンなど化学繊維は大量生産されているが、その原材料の多くは石油由来で、生分解されにくい。獣毛のような動物繊維は、ヤギやヒツジなどの飼育過程で多くの温室効果ガスを排出するとされ、綿のような植物繊維でも水の大量使用や農薬の問題がある。天然、化学にかかわらず既存の繊維の環境負荷は見逃せず、サステイナブルな暮らしのためには、衣食住の一端を担う新しい繊維の開発は欠かせない。
新しい繊維素材の開発に成功
山形県鶴岡市に拠点を置くスパイバー株式会社は、2013年、糖を主原料に、微生物による発酵生産を利用して人工クモ糸の量産技術の開発に初めて成功した企業として知られている。クモの糸は、強靱性が鋼鉄の340倍といわれ、 “地球上で最もタフな繊維”と考えられている。そのような繊維を人工的に製造できれば、さまざまな局面で環境への負荷も軽減されるはずだ。
同社が開発した人工クモ糸は「クモノス(QMONOS)」と名づけられ、アウトドアウェアメーカーのジャケットが試作された。しかし天然のクモの糸の遺伝子をベースにしたこの繊維は、まさに天然のクモの糸と同様、水に濡れると数十パーセントも縮むという超収縮性があり、厳しい自然環境で着る衣類の素材としては残念ながら適さなかった。
その開発から4年。スパイバー社では新しいタンパク質繊維の開発に成功した。
同社取締役兼代表執行役の関山和秀氏は、学生時代からタンパク質構造の研究に従事しており、クモノスの開発もその成果だ。そこで、微生物発酵という手法はそのままに、しかしクモの糸にこだわらず、目的に応じたアミノ酸配列を設計するよう、発想を切り替えた。そして開発されたのが「ブリュード・プロテイン™(醸造されたタンパク質)」、つまり微生物による発酵で製造された有用タンパク質だ。
一連の製造工程はこうだ。まず、さまざまな天然タンパク質やこれまで蓄積してきたデータを参考に、欲しいタンパク質のアミノ酸配列をデザイン、カスタマイズする。次に独自のアルゴリズムを使ってコンピュータで遺伝子配列を創出。この遺伝子を合成して微生物に導入する。培養工程で微生物が糖類などを取り込み、タンパク質が生産される。紡糸の場合、精製工程を経てできたタンパク質のポリマー(粉末)を紡糸して繊維に加工していく(図1)。
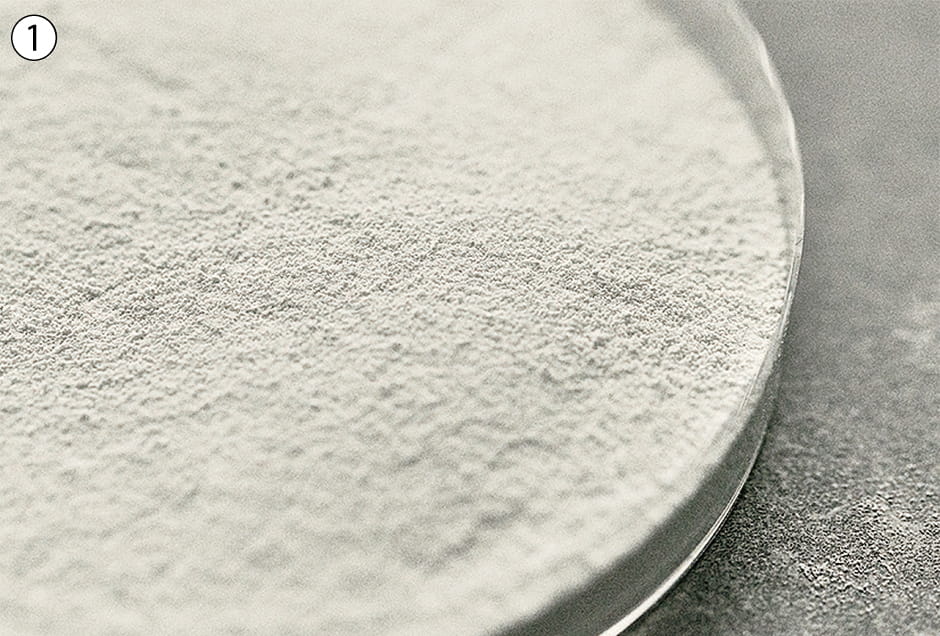
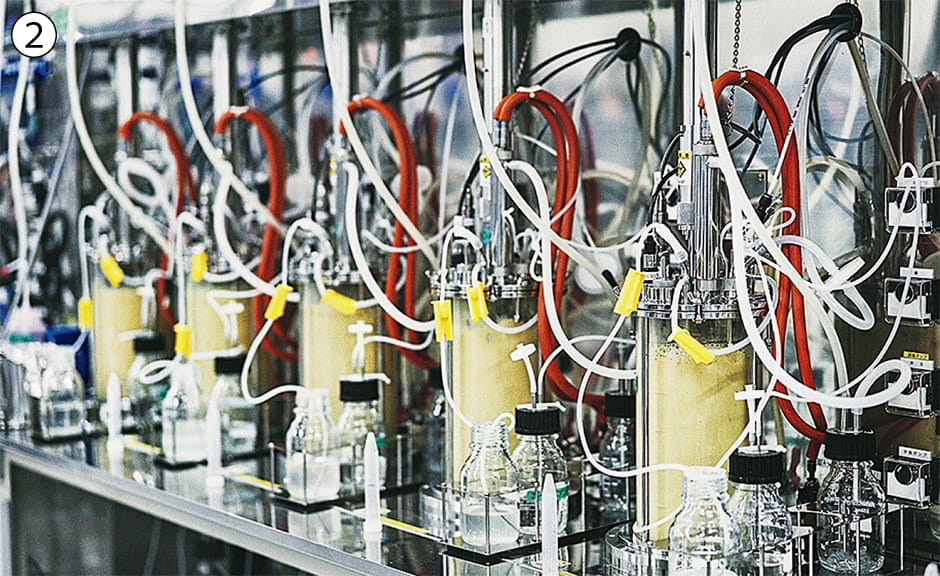
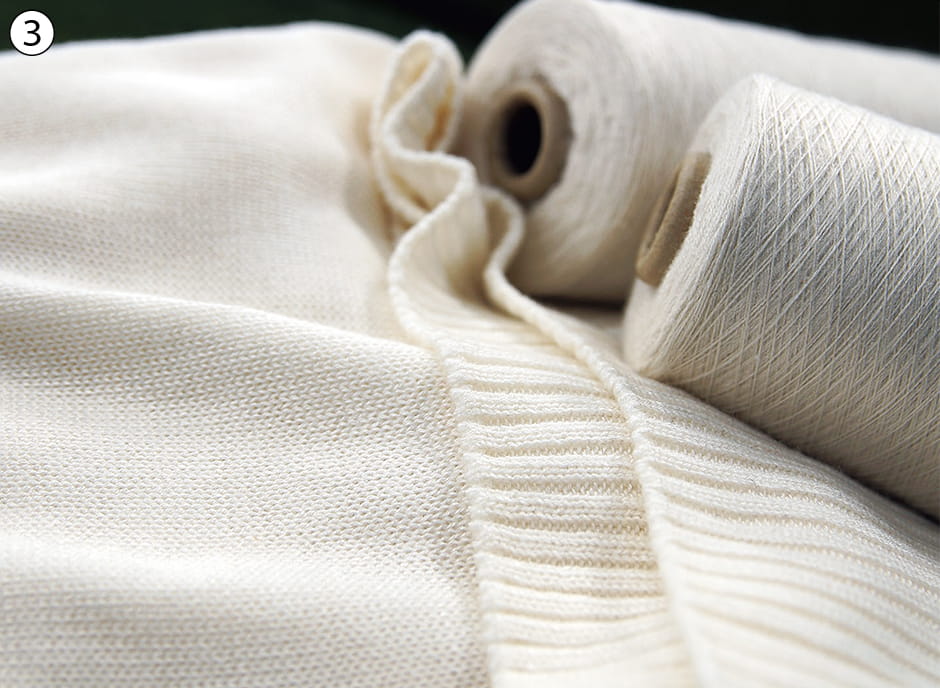
図1 微生物が作るタンパク質①ブリュード・プロテイン™のポリマー。用途やアプリケーションに応じて、さまざまな形態に加工が可能。
②スパイバー社ラボにおける小規模微生物培養装置。
③紡績糸を使用したニットサンプル。繊維径やタンパク質の含有率を変えることで、さまざまな風合いを出すことができる。
微生物を使ったタンパク質生産には、高い技術が欠かせないが、加えて紡糸工程においても、独自の技術があるという。粉末状の原料を溶解して繊維化するという大まかな流れを聞くと石油由来の化学繊維と似ているのだが、一つひとつの過程では「素材に従って、各工程を最適化する必要があります。各工程の条件が一つ違えば、当然、できあがる繊維の特性も変わってくるからです」(同社ファイバー・テキスタイル部門、製造チーム、冨樫翔太氏)と言う。タンパク質のデザインとその加工方法の組み合わせによって、さまざまな性質の繊維が製造される。
繊維の製造に微生物は欠かせない
現在は、アパレルメーカーに向けた繊維開発に注力して、アウトドアウェアメーカー、パリコレに出展しているデザイナーなどと協業している。手触りなどが好評とのことで、サステイナブルな素材が求められるファッション業界でも少しずつ存在感が増している。
ブリュード・プロテイン™素材の開発で微生物の力に注目した点について、関山氏によれば「エネルギー効率に優れ、分裂スピードがケタ違いに速い微生物なら、製造工程における省エネ化・省資源化ができ、環境負荷や生産コストも最小限に抑えられると考えた」と言う。
開発までに複数の微生物で実験を重ねたが、生産効率、安定性などから厳選され、最終的に“精鋭”の1種が選ばれた。ブリュード・プロテイン™繊維は、現在はTシャツやカシミヤ風ニットなどで使われ、これらの製造の範囲ではターゲットとなるタンパク質が変わっても、発酵を担う微生物は変わらない。しかし人工レザー、人工ファーや、人工毛髪の開発、さらに自動車の部材などに利用される炭素繊維複合材料や医療分野で使用される製品では、ターゲットに応じてタンパク質の産生を担う微生物を検討する可能性もあるという(図2)。
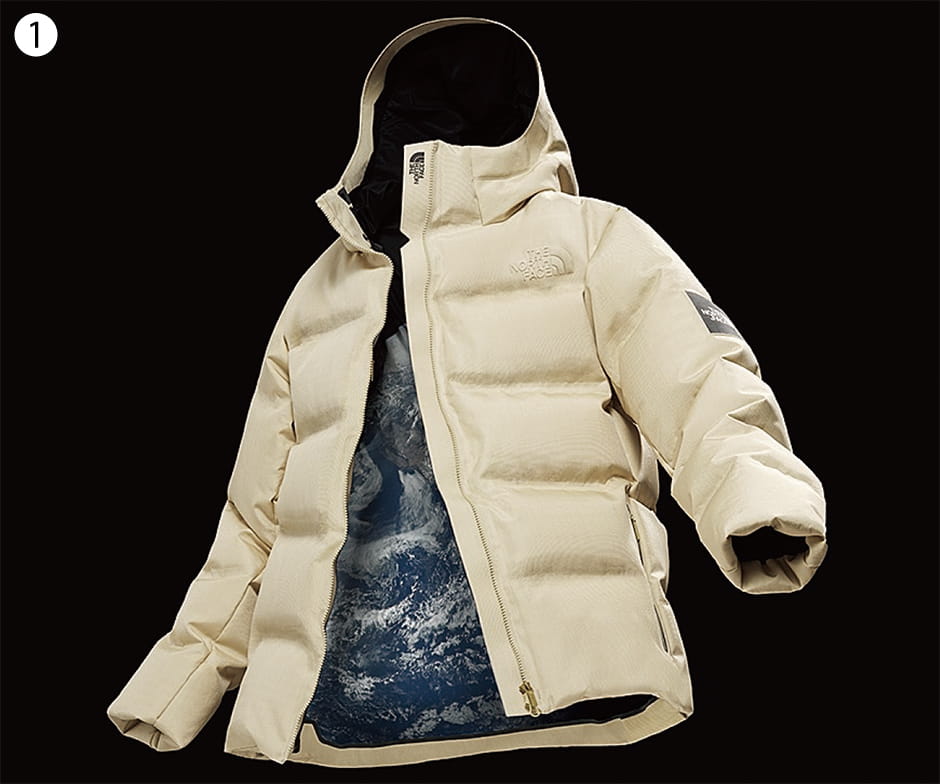
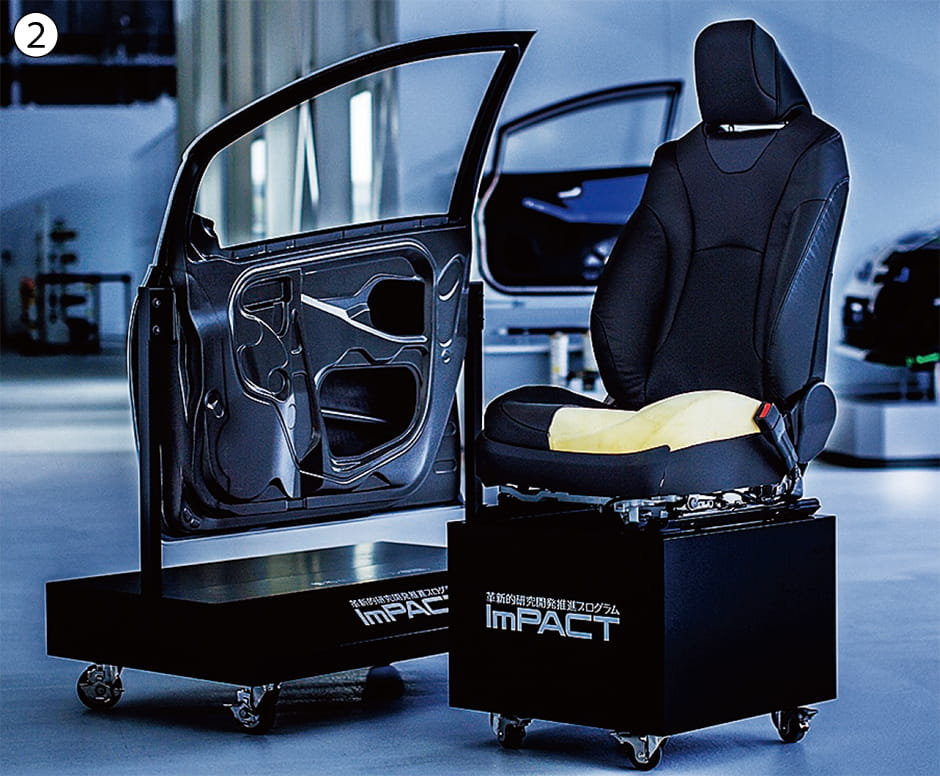
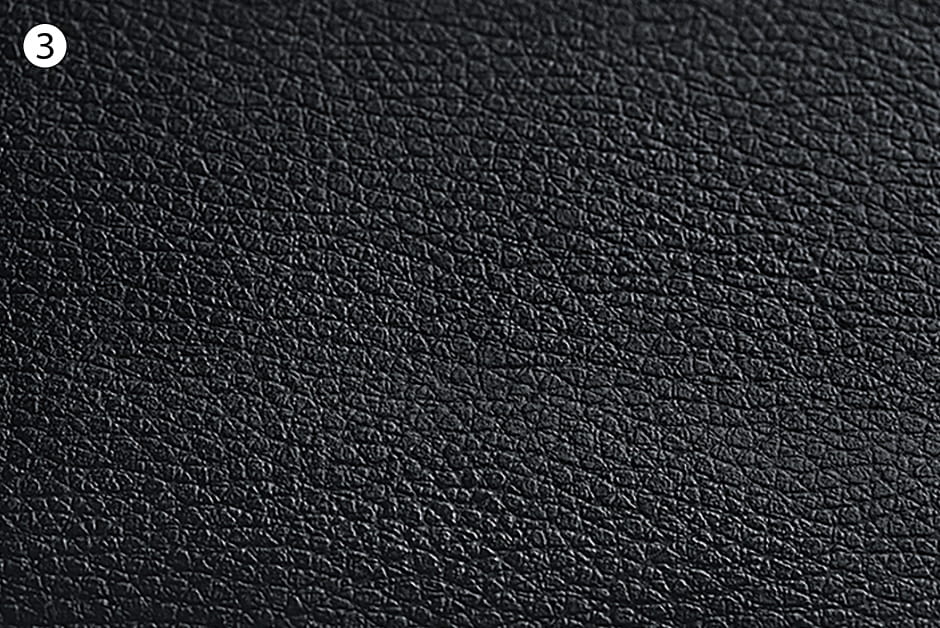
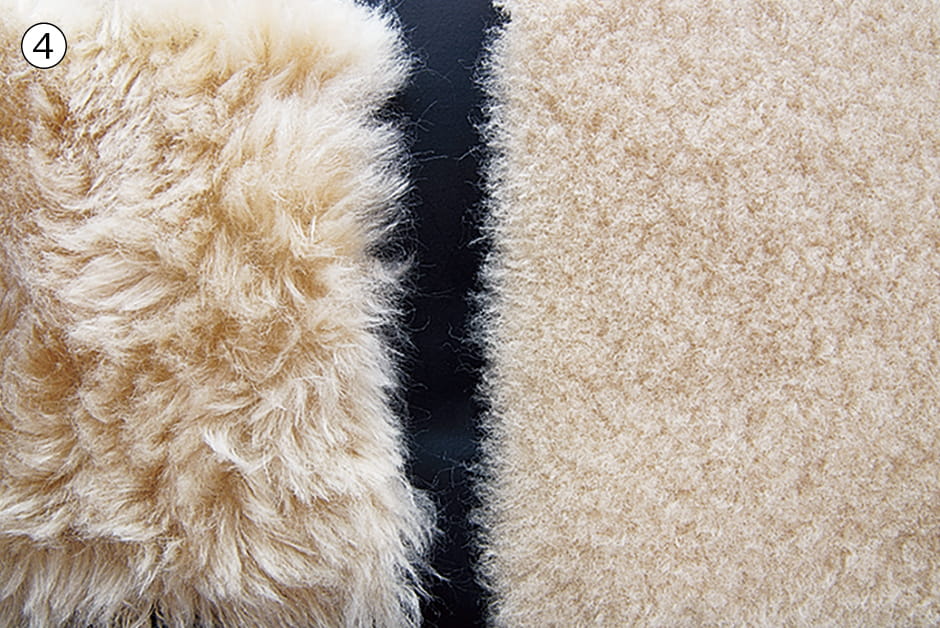
図2 人工構造タンパク質を用いた製品①株式会社ゴールドウインとの共同研究開発による商品。人工構造タンパク質を使った世界初のアウトドアジャケット「MOON PARKA」(*MOON PARKAはスパイバー社とゴールドウイン社の商標)。
②内閣府が推進する革新的研究開発推進プログラム(ImPACT)における参画企業との共同成果物(画像提供:ImPACT)。
③ブリュード・プロテイン™をポリマー加工して成形したレザー風サンプル。
④短繊維状のブリュード・プロテイン™繊維を加工し、ファーのような風合いを出したサンプル。
同社の担当者が思わず「微生物に作って “いただいて”」と口にしてしまうように、サステイナブルな繊維の製造に微生物は欠かせない戦力となっている。
微生物の分解発酵によって産生した物質を利用することもあれば、分解の力を借りて、環境に負荷をかけずに衣類を廃棄しようという試みもある。
大阪に本社を置く繊維卸売りの株式会社V&A Japanでは、衣類に使える生分解性のポリエステル「ReTE」を開発した。堆肥中の微生物が酵素を分泌し、H2O、発酵熱が作用してポリエステルに加水分解が起こり、低分子化、さらに分解されて土に返るまでの仕組みを整えた。
先にポリエステルについて簡単に説明しておきたい。「ポリエステル」の種類は多岐にわたっている。大まかには衣類などに使われる繊維としてのポリエステルと、PET(ポリエチレンテレフタレート)ボトルなど成形品のポリエステルがある。ちなみにフリースに使われるポリエステルは、後者だ。
ポリエステルは合成繊維の中で生産量が最も多く、スポーツ用のウェアからワイシャツ、下着までさまざまな種類の衣類に使われている。摩耗に強く耐久性、速乾性があり、軽く、シワになりにくいと、優れた機能を持つ繊維なので利用範囲も広い。これだけ衣類に重宝されるのは、繰り返し洗濯し、アイロンをかけ、タンブルドライして、日光に曝されるという使われ方にも、十分耐える素材だからだ。
そして、こうした耐久性という特徴と、生分解性という、ある種相反する特徴を両立させたのが、同社の素材だ。
特定堆肥中生分解性ポリエステル
実は「生分解性ポリエステル」(ポリ乳酸)は、他にいくつも存在する。使い捨ての食品容器などに使われており、市場では「生分解性プラスチック」として通っていたり、生体内で溶けて抜糸の必要のない糸は手術に利用されたりしている。これらの素材は、一定の期間が過ぎれば不要になる、捨てることが前提なので、耐久性はあまり問われない。各国に「生分解性」の認証機関があり、生分解性や金属性などの項目で一定の基準をクリアすることが条件になっている。例えば生分解性は微生物が産生する炭素量を基準としているが、日本では試験開始時から6カ月以内に炭素が60%以上増加、海外では90%以上増加することを基準にしている国もある。
一方、同社の製品は、洗濯もアイロンがけも従来の素材と変わらずにできるが、ほとんど分解されるのに12カ月程度かかる。そのため同社の製品は「特定堆肥中生分解性ポリエステル」と謳っている(図3)。
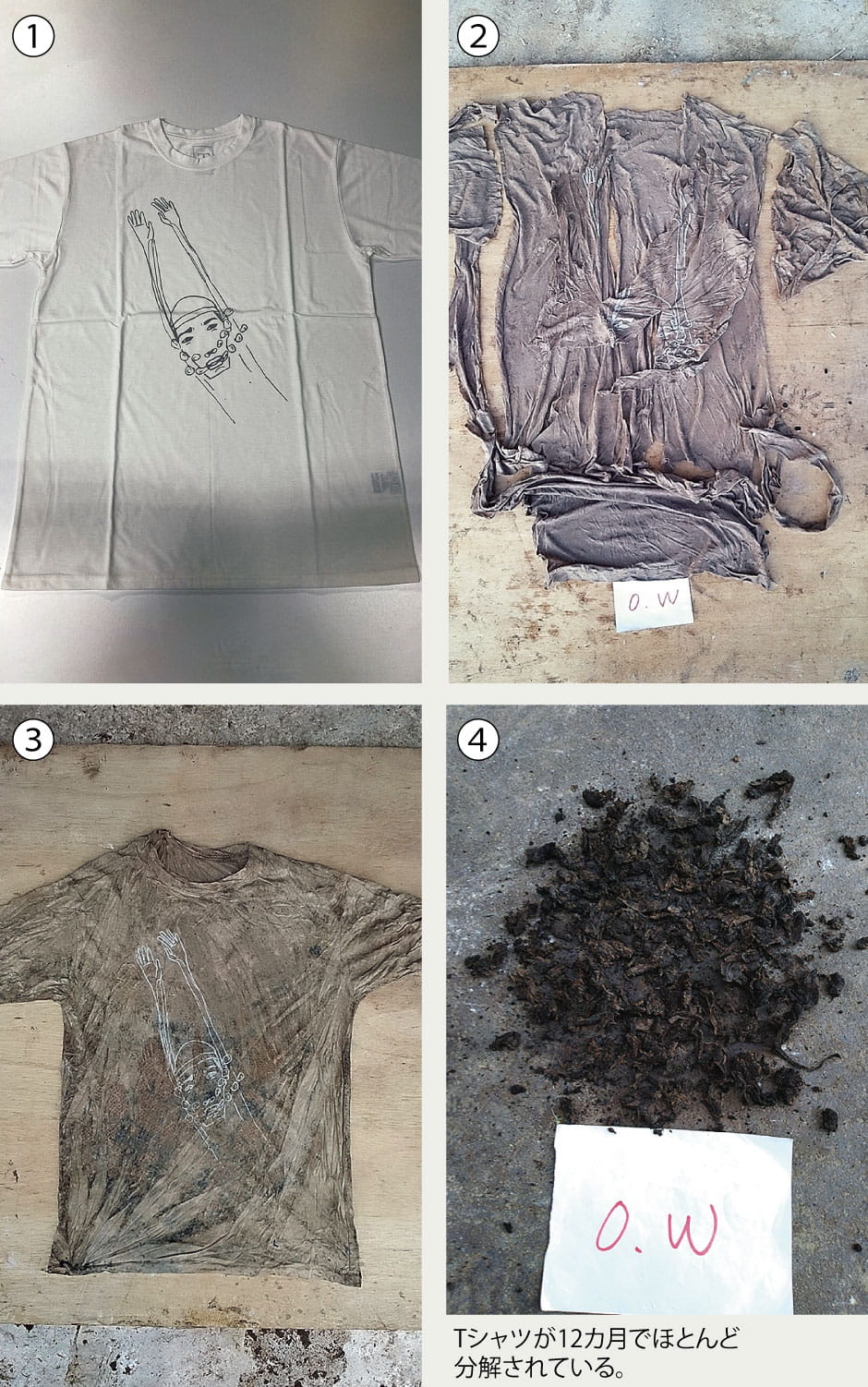
図3 堆肥施設での分解実験
ここで「特定」としているのにも理由がある。生分解性を目指して開発している製品なので、分子の構造を研究すると同時に、分解する場所についても試行錯誤を繰り返したという。嫌気的な土地、養豚場、さらに畑や花壇などでも実験をしたが、最終的に決まった場所が酪農場を兼業する堆肥施設だった。
「いろいろな場所で実験をしたのですが、思い通りの結果が出る場所は他にありませんでした」(同社テキスタイル販売事業部・真木佐和子氏)
この堆肥施設では、牛糞や塵芥なども集め、それを原料に堆肥を作っている。堆肥は毎日攪拌するので好気的となり、牛糞など微生物のエサも毎日追加される。堆肥の温度は発酵によって60~80℃ほどにまで上がるという。
同社の製品は、高分子の研究者と共同で開発しており、樹脂の構造から耐久性と生分解性の特徴を実現したのだが、分解する微生物は特定されていない。別の場所で同じ土を使って分解実験をしたそうだが、ほとんど分解されないとのこと。堆肥施設は管理が行き届いて、微生物が活発に育つ環境が整っているということだろう。
同社の取り組みの特徴は、この製品を販売するだけでなく、回収、分解するところまで仕組みをつくったことだ。同社の繊維を使った衣類が不要になったら、販売店や同社などが回収し、施設での分解を見届ける。見た目だけでは他のポリエステルと区別がつかないので、衣類には専用のタグを付けることになっている。
最後の分解まで見届ける
この取り組みに賛同し、自身のブランドで同社の素材だけを使った「コンポスタブルシリーズ」(図4)を立ち上げたデザイナーもいる。「たくさんの資源を使ってきたファッションの世界でも、サステイナブルについて考えることが必要です。同社の試みに共感すると同時に、デザイナーにとっては、加工の制限が少なく、伸び伸びとデザインできるポリエステルという素材を使って、環境への負荷を軽減できるのはうれしい」(「wmg.」デザイナー・坂寄順子氏)
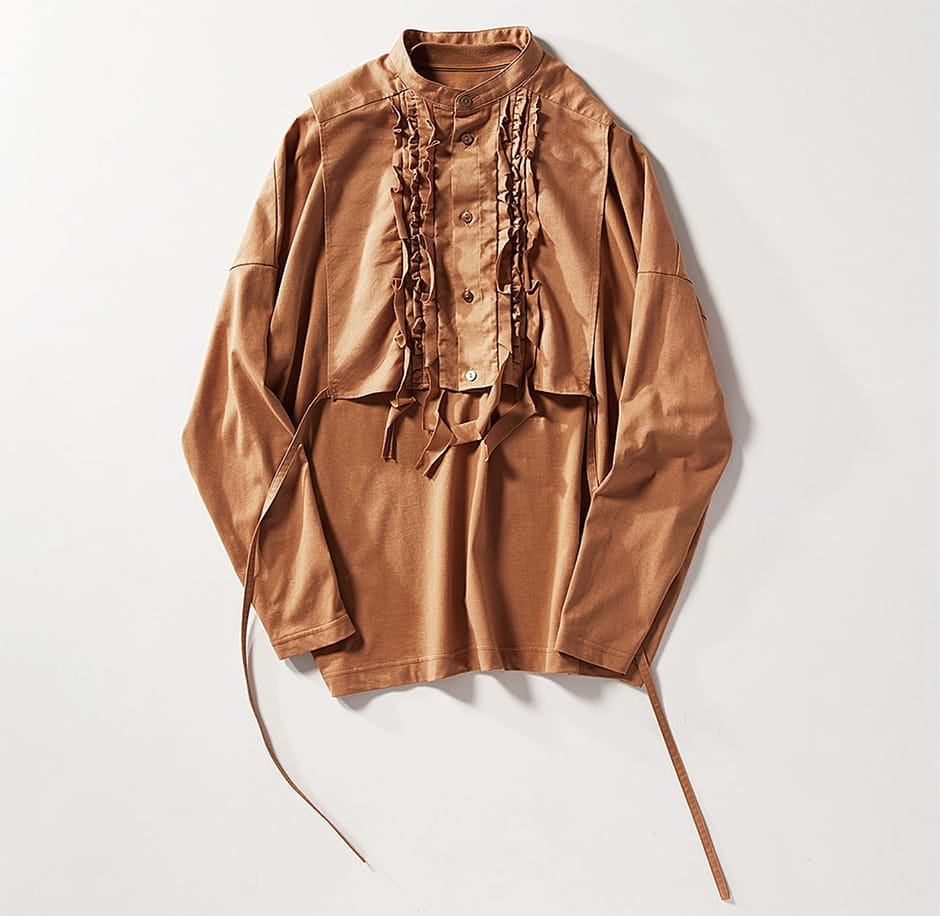
図4 生分解するポリエステルを使ったプルオーバー坂寄順子氏は素材に惚れ込み、コンポスタブルシリーズを立ち上げた。
なぜ同社は最後の分解まで見届けようとしたのか。
実は「生分解性」素材といっても、どんな場所でも生分解されるわけではなく、素材によって、海洋で分解する、埋め立て地で分解するなど、分解される場所が決まっていることがある。さらには、同じ埋め立て地でも嫌気性と好気性があり、それだけでも生息する微生物が違う。微生物が違えば好むエサも異なり、分解するものも違う。つまり生分解性の素材だからといって自然環境ならどこでも分解されるわけではなく、嫌気性の土壌を好む微生物が分解する素材は、好気性の土地では分解されない可能性も高い。だが、消費者にそこまでの事情は理解されていないことも多いので「生分解性」というと、漠然と「土に返るんだな」と思いがちだ。
「せっかく生分解性の素材を作ったのだから、きちんと最後まで責任を持ちたいと思ったのです。消費者の方々にも衣類の素材について、知ってもらえたらいいと思っています」(真木氏)。
サステイナブルな環境は、微生物の力を借りると同時に、やはり私たちが意識を変えないことには成り立たない。